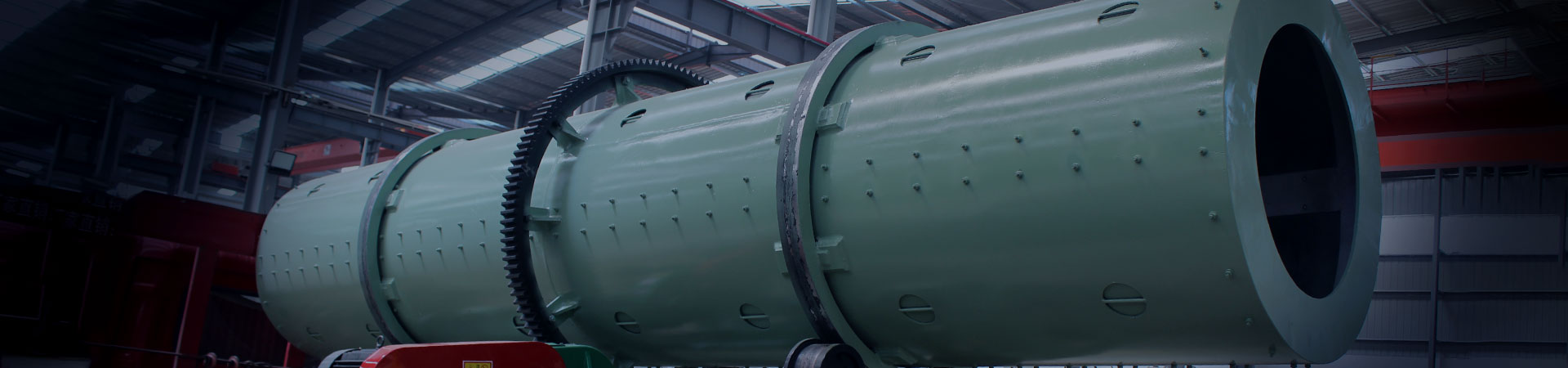
Ring mold granulator is an efficient and widely used granulation equipment, mainly used in industries such as biomass fuel, feed, chemical raw materials, etc. It forms particles with specific sizes and shapes by extruding powdered or small granular materials through the holes of a circular mold under high pressure, in order to improve the performance and storage and transportation convenience of the materials.
The ring mold granulator is widely applicable to:
Biomass fuel: granulation of biomass materials such as sawdust, straw, rice husks, etc.
Feed industry: production of poultry, livestock, and aquatic feed.
Chemical industry: granulation of fertilizers, catalysts, additives, etc.
Pharmaceutical industry: pre-treatment of tablet and capsule filling materials.
The ring mold granulator mainly includes the following key components:
Ring mold: A circular mold with holes, which is a key component for material forming, usually made of wear-resistant alloy steel.
Pressure roller: a rotating roller that applies high pressure to the material through rotation, forcing the material to pass through the ring mold hole.
Feeding system: used to evenly feed materials between the pressure roller and the ring mold.
Drive system: including motor, reducer, etc., providing power for the pressure roller.
Cooling system: used to cool the material after granulation to stabilize the particle structure.
Crushing system: used to crush large pieces of material or adhered particles into the desired size.
Control system: Monitor and adjust equipment operating parameters, such as pressure, temperature, speed, etc., to ensure the stability and particle quality of the granulation process.
High pressure molding: Through high-pressure extrusion, materials that are difficult to cure can be effectively molded, resulting in good molding effects.
Wide applicability: Strong adaptability to materials, able to handle various properties of powdered or small particle materials.
Particle uniformity: By precisely controlling the pressure and mold hole size, particles with regular shapes and uniform sizes can be produced.
Continuous production: capable of achieving continuous material feed and particle output, with high production efficiency.
Moderate energy consumption: Compared to other granulation methods, the energy consumption of the ring mold granulator is relatively low.
Compact structure: The equipment has a reasonable structural design, occupies a small area, and is easy to maintain and operate.
Environmental protection and energy conservation: The granulation process produces less dust and low noise, meeting environmental requirements.
High pressure molding: Through high-pressure extrusion, materials that are difficult to cure can be effectively molded, resulting in good molding effects.
Wide applicability: Strong adaptability to materials, able to handle various properties of powdered or small particle materials.
Particle uniformity: By precisely controlling the pressure and roller gap, particles with regular shapes and uniform sizes can be produced.
Continuous production: capable of achieving continuous material feed and particle output, with high production efficiency.
Low energy consumption: Compared to other granulation methods, the energy consumption of the roller extrusion granulator is relatively low.
Compact structure: The device has a relatively simple structure, occupies a small area, and is easy to maintain and operate.
Environmental protection and energy conservation: The granulation process produces less dust and low noise, meeting environmental requirements.
We are a high-quality manufacturer of organic fertilizer equipment Providing excellent consultation and after-sales service
© Copyright 2024 Huaqiang All rights reserved.